
SCHULER ARTS
CREATVITY RETREAT CENTER
1201 Maple St
Albion, Mi
Phone: (517)629-8293
Email: schulerarts@gmail.com
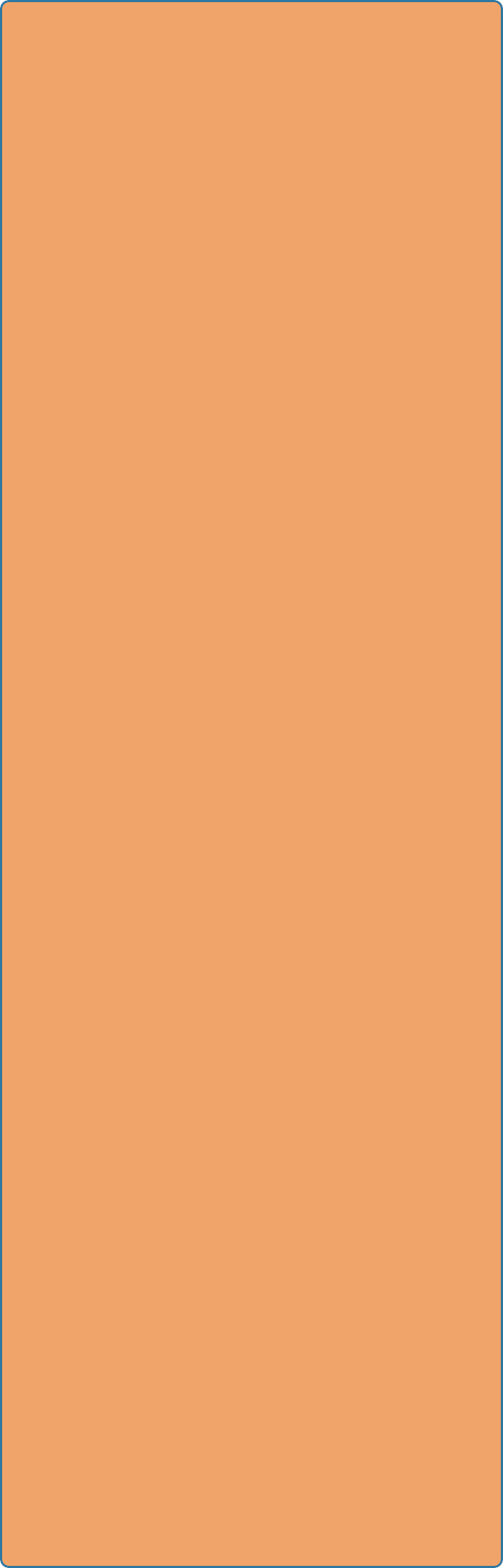
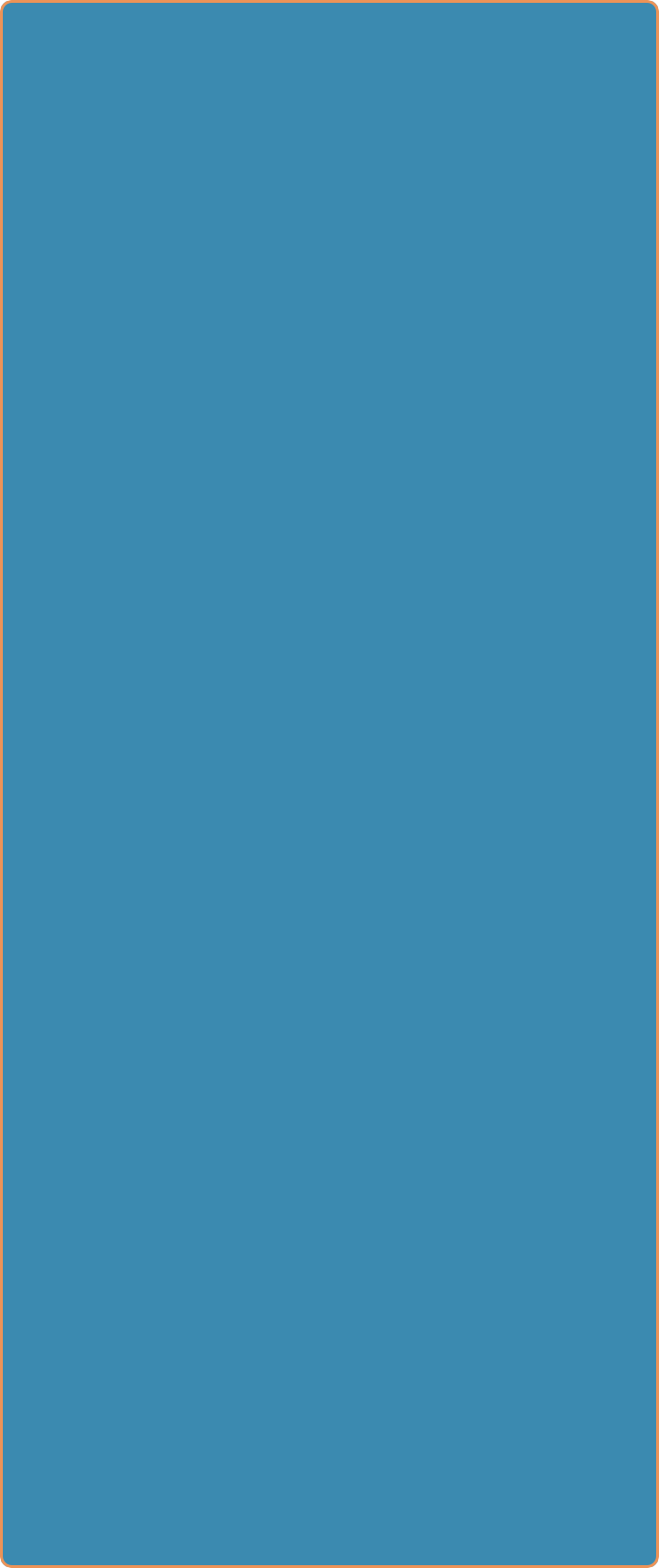
RAKU HISTORY
Raku Pottery was developed in Japan in the early 1500’s as the Ceremonial Tea Ware of the Zen Buddhist Masters. The word Raku is interpreted to mean enjoyment, serenity, contentment and freedom. It was preferred by the Masters because of its humility, tasteful unpretentiousness, simple naturalness, and its deliberate avoidance of luxury...all very important to the Zen philosophy.
Although contemporary artists have radically altered traditional Raku methods, many still refer to their new alternative firing techniques as Raku. It is a low-fired ware that is quite porous and seldom watertight. Raku’s primary utility or function is its elusive, subtle, yet vigorous beauty and therefore, must be approached with a different criterion in mind, like a painting or a symphony.
RAKU PROCESS
A bisqued (once-fired unglazed) pot is first coated with glaze and placed into a kiln. The kiln is then heated rapidly to about 1,900 degrees. It is this initial tremendous heat shock that often causes "body cracks" in the clay wall of a pot or even makes it explode. If the vessel survives this shock, almost immediate metamorphosis begins. The entire vessel glows red-hot and the glaze becomes molten glass.
At this point, the pot must endure a second shock as long-handle tongs are used to remove the glowing form from the inferno. As the cool air outside the kiln hits the glowing vessel, the severe temperature change may produce cracks in the glaze. These cracks are highly prized as characteristic of traditional Raku Pottery -- they are the "proof-marks" that the vessel survived this dramatic trial by fire.
Upon leaving the kiln, the gleaming pot is placed directly into an airtight container (a metal trash can) filled with combustible material (newspapers, sawdust, leaves, straw or wood chips). The unglazed areas smoke to a soft gray or black often highlighting the valued cracks in the glaze. Metallic oxides in the glaze become lustrous and are frequently brilliant in color. As if all this is not enough, the vessel (often still over 1,000 F) may then be plunged into cold water to halt the process and then finally cleaned with a hard bristle brushed or steel wool. And so the earth, fire, air and water process is complete.
OUR PERSPECTIVE
The Raku Workshop experience for us at Schuler Arts is a dynamic venue for creative expression, personal growth, social interaction and spiritual connection. This extraordinary art event is exciting and fun to experience through active participation and collaboration in every phase of the artistic development and creative firing process. We hope that your Raku Workshop will rekindle your sense of passion, awe, and wonderment that is your natural, God-given condition.
GLASS FUSING HISTORY
While the precise origins of glass fusing techniques are not known with certainty, there is archeological evidence that the Egyptians were familiar with techniques ca. 2000 BCE. Although this date is generally accepted by researchers, some historians argue that the earliest fusing techniques were first developed by the Romans, who were much more prolific glassworkers. Fusing was the primary method of making small glass objects for approximately 2,000 years, until the development of the glass blowpipe. Glassblowing largely supplanted fusing due to its greater efficiency and utility.
While glass working in general enjoyed a revival during the Renaissance, fusing was largely ignored during this period. Fusing began to regain popularity in the early part of the 20th century, particularly in the U.S. during the 1960s. Modern glass fusing is a widespread hobby but the technique is also gaining popularity in the world of fine art. All of these techniques can be applied to one glass work in separate firings to add depth, relief and shape.
FUSING PROCESS
Most contemporary fusing methods involve stacking, or layering thin sheets of glass, often using different colors to create patterns or simple images. The stack is then placed inside the kiln (which is almost always electric, but can be heated by gas or wood) and then heated through a series of ramps (rapid heating cycles) and soaks (holding the temperature at a specific point) until the separate pieces begin to bond together. The longer the kiln is held at the maximum temperature, the more thoroughly the stack will fuse, eventually softening and rounding the edges of the original shape. Once the desired effect has been achieved at the maximum desired temperature, the kiln temperature will be brought down quickly through the temperature range of 815 °C (1,499 °F) to 573 °C (1,063 °F) to avoid devitrification. The glass is then allowed to cool slowly over a specified time, soaking at specified temperature ranges which are essential to the annealing process. This prevents uneven cooling and breakage and produces a strong finished product.
This cooling takes place normally for a period of 10–12 hours in 3 stages. The first stage- the rapid cool period is meant to place the glass into the upper end of the annealing range 516 °C (961 °F). The second stage- the anneal soak at 516 °C (961 °F) is meant to equalize the temperature at the core and the surface of the glass at 516 °C (961 °F) relieving the stress between those areas. The last stage, once all areas have had time to reach a consistent temperature, is the final journey to room temperature. The kiln is slowly brought down over the course of 2 hours to 371 °C (700 °F), soaked for 2 hours at 371 °C (700 °F), down again to 260 °C (500 °F) which ends the firing schedule. The glass will remain in the closed kiln until the pyrometer reads room temperature.
Note that these temperatures are not hard and fast rules. Depending on the kiln, the size of the project, the number of layers, the desired finished look, and even the brand of glass, ramp and soak temperatures and times may vary. Small pendants can be fired and cooled very rapidly. For instance, small glass pieces can be fired in as little as one hour. According to Paragon Industries, the QuikFire can reach 537 °C (999 °F) in five minutes.
OUR PERSPECTIVE
The Glass Fusing Workshop experience for us at Schuler Arts is a dynamic venue for creative expression, personal growth, social interaction and spiritual connection. This extraordinary art event is exciting and fun to experience through active participation and collaboration in every phase of the artistic development and creative process. We hope that your Glass Fusing Workshop will rekindle your sense of passion, awe, and wonderment that is your natural, God-given condition.


* SPARK your creative side...